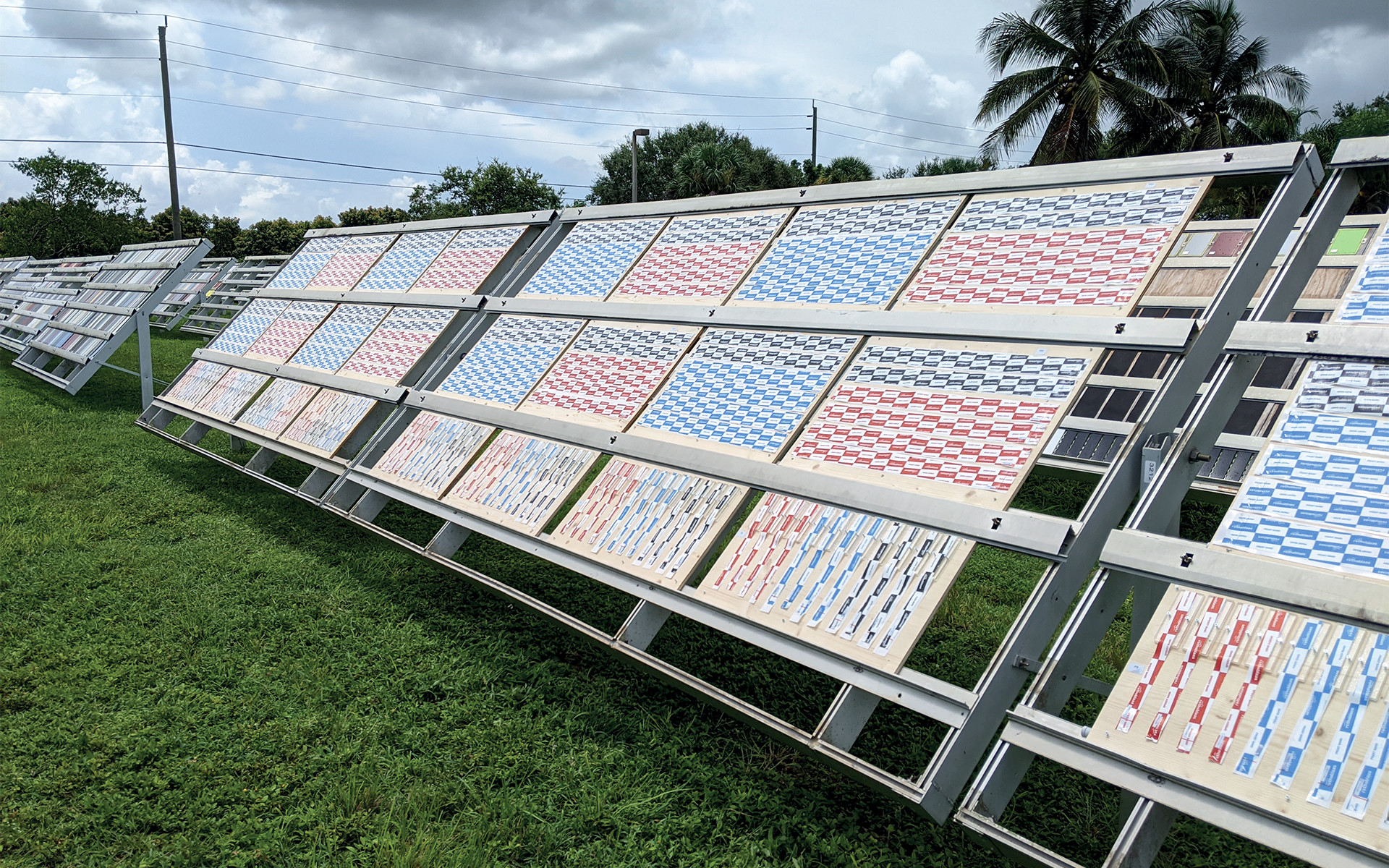
Durability testing in real-world conditions and in the laboratory
Despite their widespread use, certain products such as adhesive tapes and membranes for energy efficiency rely on UNI EN ISO standards, which fail to provide clear indications regarding the durability (membranes) or adhesion (tapes) of the material following prolonged exposure to UV radiation and weathering.
Regarding membranes, the European UNI EN 13859 standard for CE marking requires only that the water tightness class be maintained after ageing, without considering the performance values that we, on the other hand, tested as part of the European MEZeroE* project.
Current standards for material ageing by UV and heat exposure involve laboratory tests that do not always correlate well with real-world conditions (artificial ageing vs natural ageing).
But what happens when tapes and membranes experience prolonged exposure to various types of environmental conditions and stresses?
It’s not uncommon for products to encounter stress during construction delays or in adverse weather conditions. To better understand the behaviour of certain Rothoblaas products, we conducted real-world tests in one of the most extreme climates in the world: Florida.
Additionally, to assess mechanical strength, adhesion strength and potential issues arising from product degradation, we performed a durability testing campaign on adhesive tapes, tape-membrane-tape joints, and a specific membrane in collaboration with the University of Cracow as part of the European MEZeroE project.
Durability testing in real-world conditions and in the laboratory
To assess specific properties such as adhesion and tensile strength, Rothoblaas tapes and certain membrane-tape combinations were subjected to various tests to evaluate changes in the materials and their properties due to exposure:
Weathering resistance testing in Florida
SPEEDY BAND adhesive tape
FLEXI BAND adhesive tape
UV and heat exposure tests conducted as part of the MEZeroE project in collaboration with the University of Cracow
1.Connection consisting of FLEXI BAND UV adhesive tape and TRASPIR EVO UV 115 membrane
2.Connection consisting of SMART BAND adhesive tape + TRASPIR EVO 160 adhesive membrane
3.TRASPIR EVO UV 115 adhesive membrane
Real-world exposure and disassembly testing
TRASPIR EVO UV 210 adhesive membrane (and TRASPIR EVO 300, which has the same properties as UV 210)
Durability testing in Florida
To evaluate specific properties such as adhesion and tensile strength, Rothoblaas tapes were exposed to the elements in Florida, followed by laboratory testing to assess the changes caused by weathering.
Florida is the only true subtropical region in the United States and is internationally recognised for its exposure to the elements: it has average monthly temperatures above 20°C year-round, monthly humidity levels that never drop below 70%, heavy rainfall during the summer/autumn period, limited rainfall in winter/spring, and relatively high UV exposure throughout the year (>20 KJ/m² with peaks of 35 MJ/m² in summer).
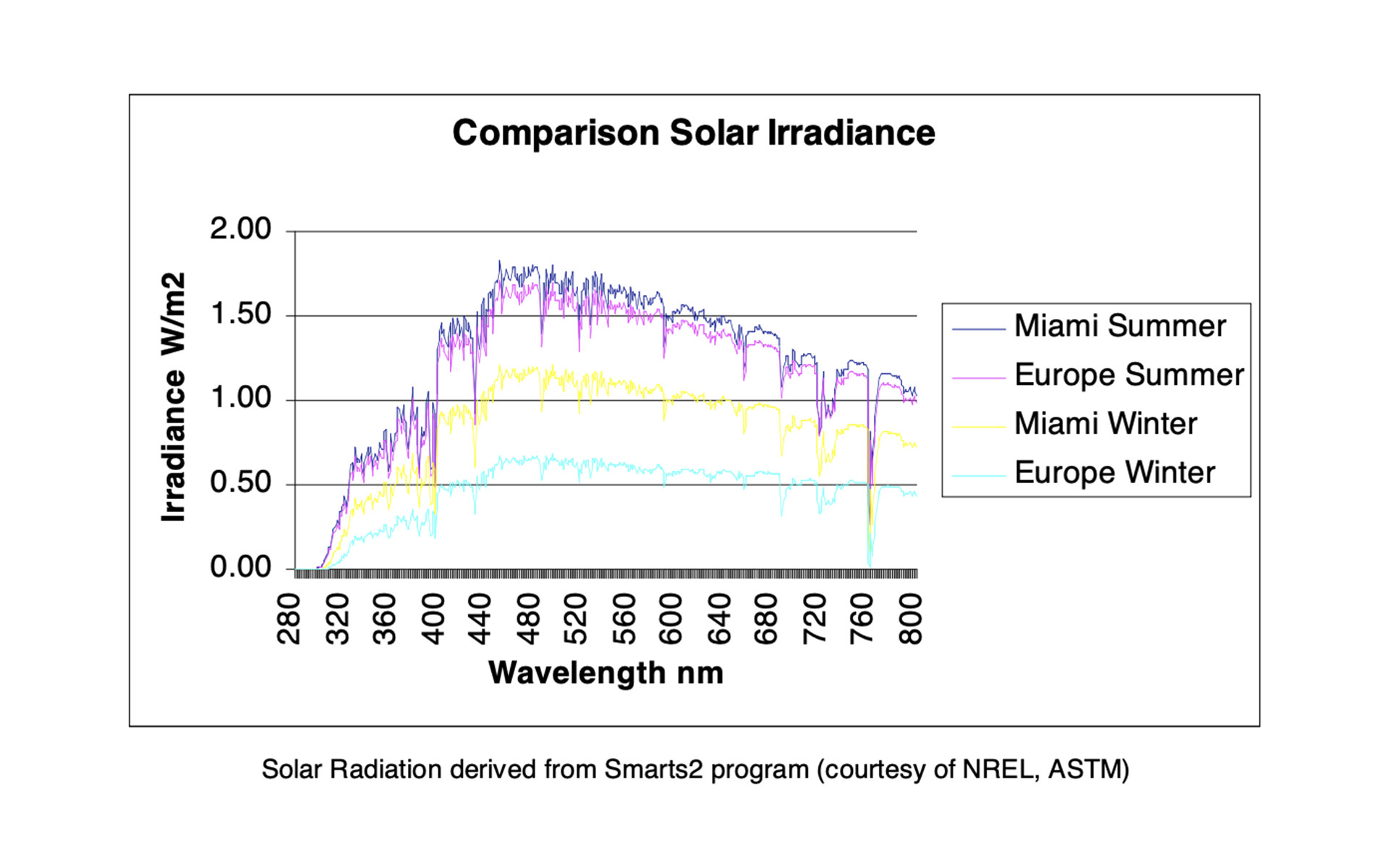
Technical characteristics of the tested products and results of “Florida weathering” tests
The SPEEDY BAND and FLEXI BAND tapes were exposed to Florida’s climate for varying periods ranging from 30 days to 3 years.
They were then tested and compared with standard tapes. Exposure in Florida is comparable to a much longer period in other parts of the world (for example, 12 months in Florida is equivalent to over 12 months elsewhere).
Tape properties
1. SPEEDY BAND: tape with PE support, solvent-free UV-crosslinked acrylic glue and reinforcing layer made of PE grid.
2. FLEXI BAND: PE support, acrylic dispersion glue without solvents and reinforcing layer made of PL grid.
Tests performed
Tensile strength and elongation at break point according to EN ISO 29864 (method B).
Adhesion strength according to EN ISO 29862 (90° angle).
Tests were performed on both non-aged and aged samples, with ageing periods of varying length (1, 2, 3, 4, 6, 8, 10, 12, 18 months).
Tensile tests
SPEEDY BAND
SPEEDY BAND satisfied all requirements in the material durability test campaign.
After 12 months of exposure to Florida's climate – marked by high temperatures, high humidity and intense exposure to UV radiation – the tape exhibited excellent ageing resistance. Despite the discolouration due to UV exposure, it maintained stable adhesion levels and a tensile strength exceeding 60% of the initial values.
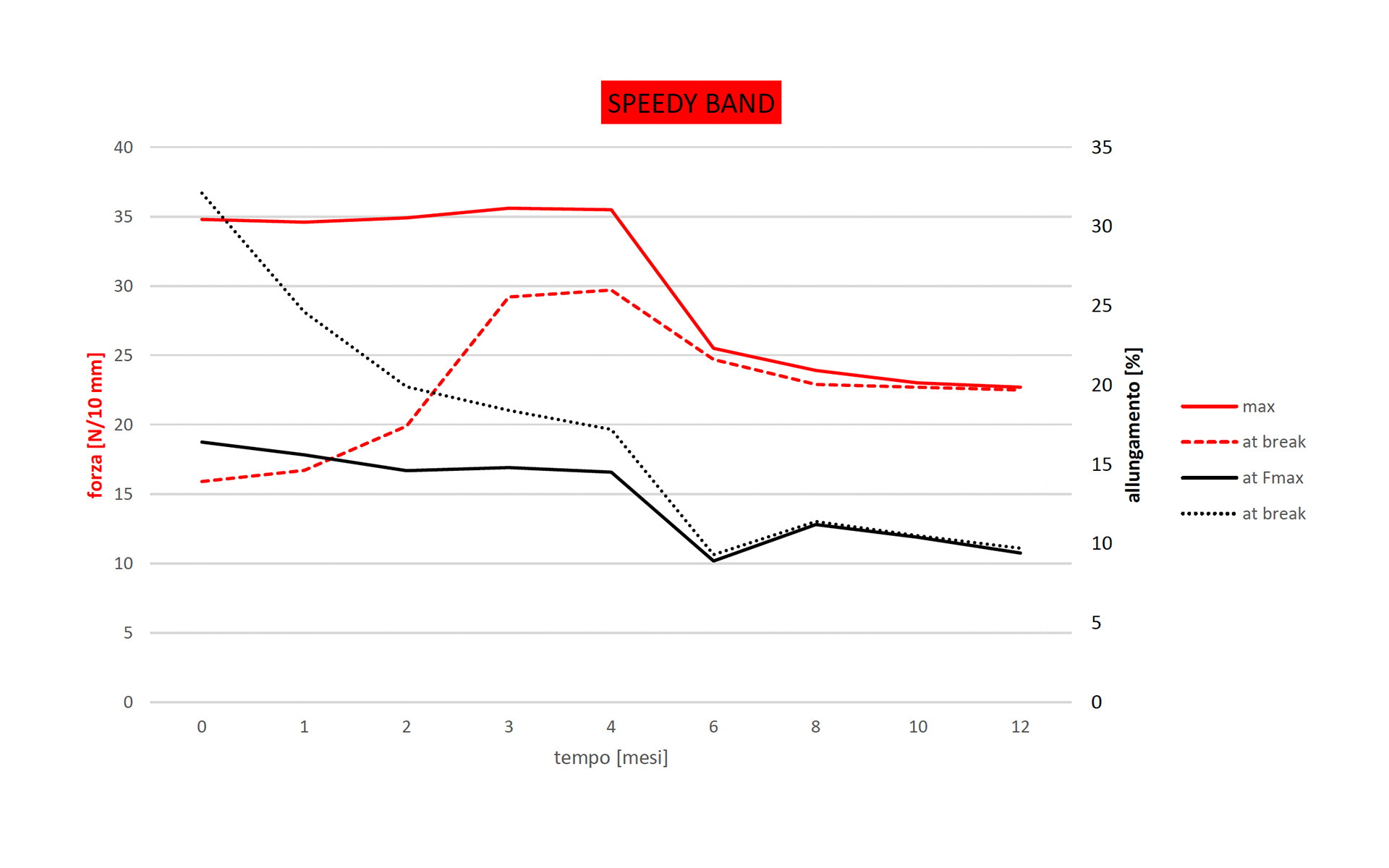
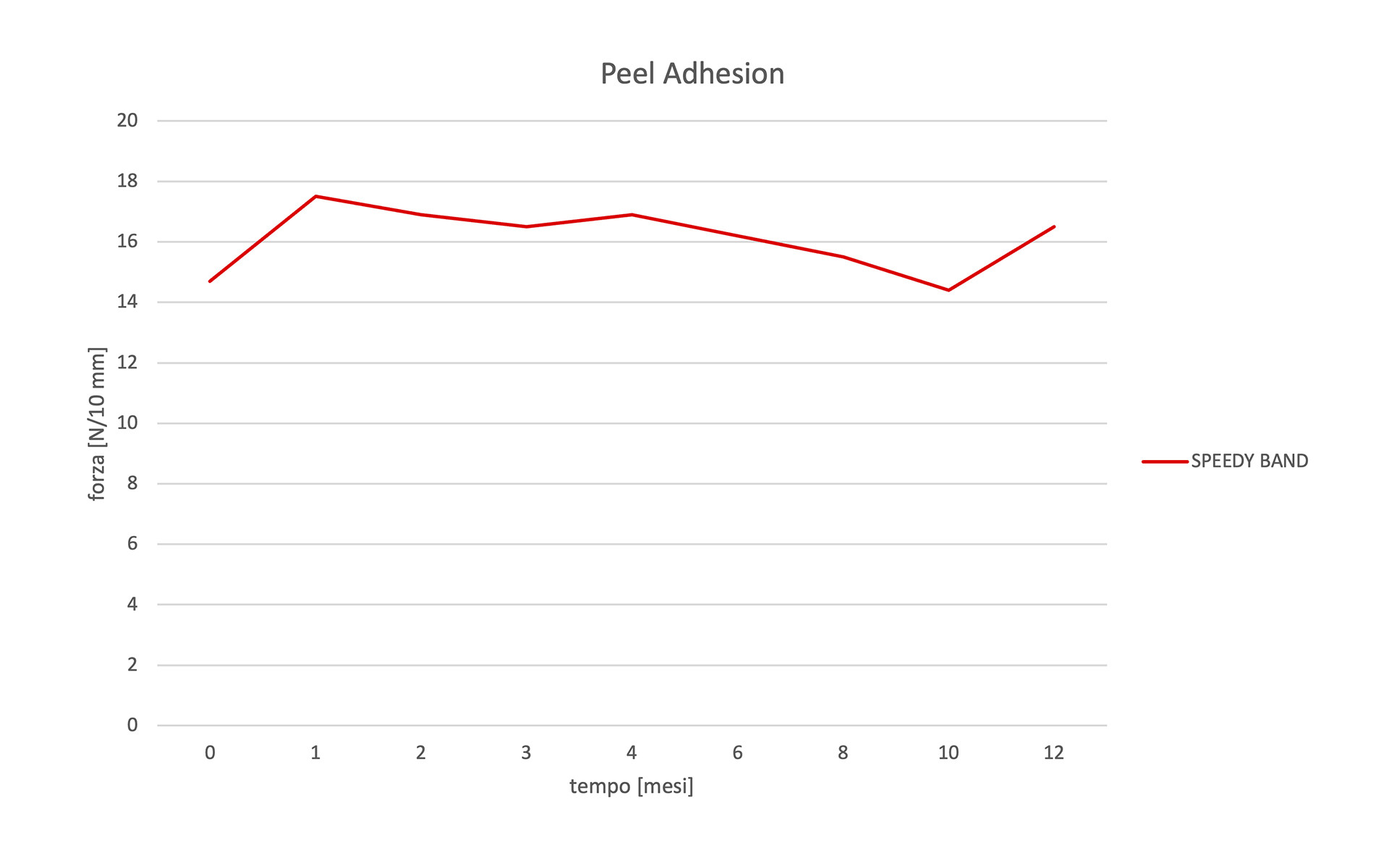
FLEXI BAND
Compared to SPEEDY BAND, FLEXI BAND retains its resistance properties for up to 6 months, with an Fmax similar to that of the non-aged tape, despite losing much of its plastic deformation after 4 months.
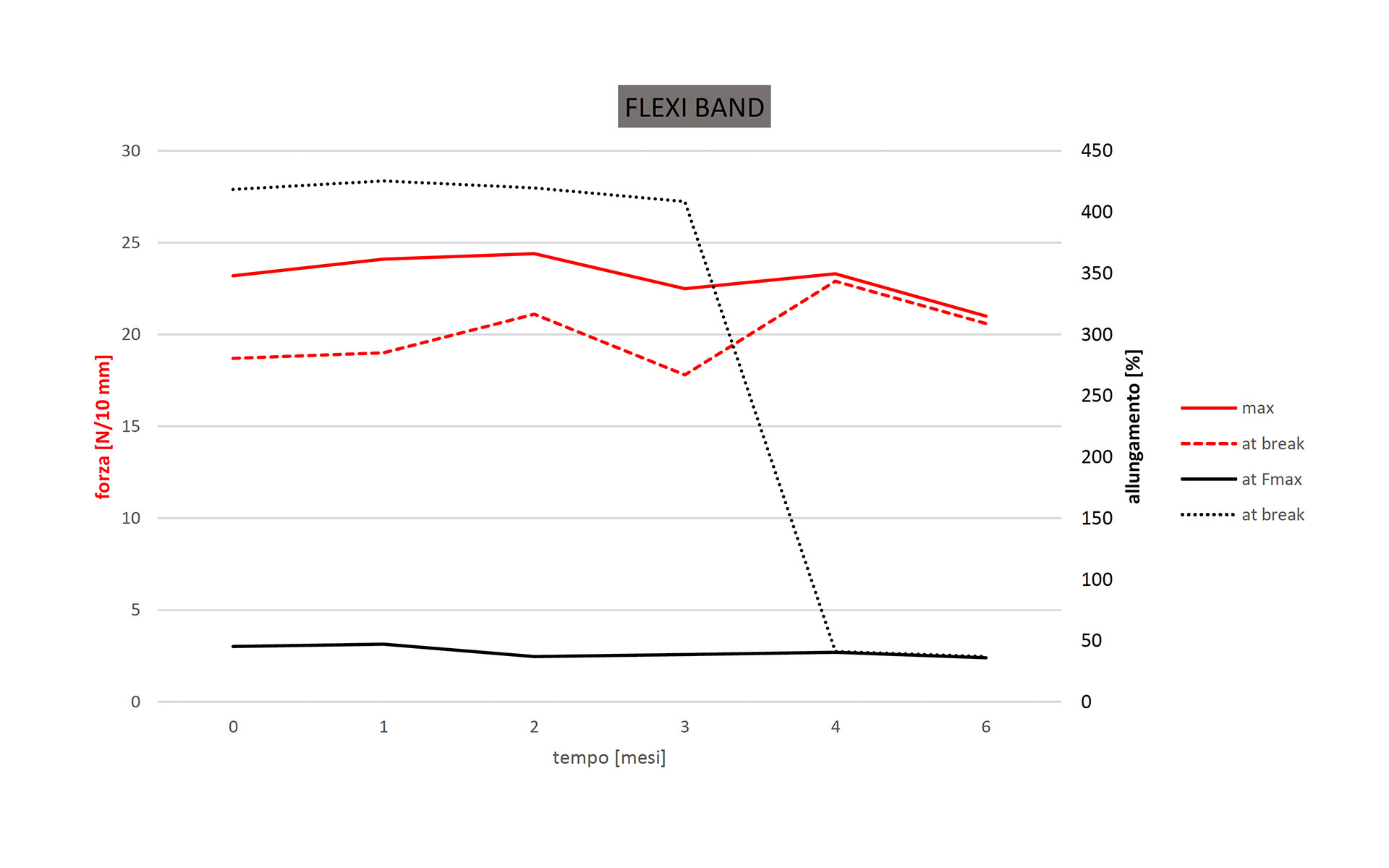
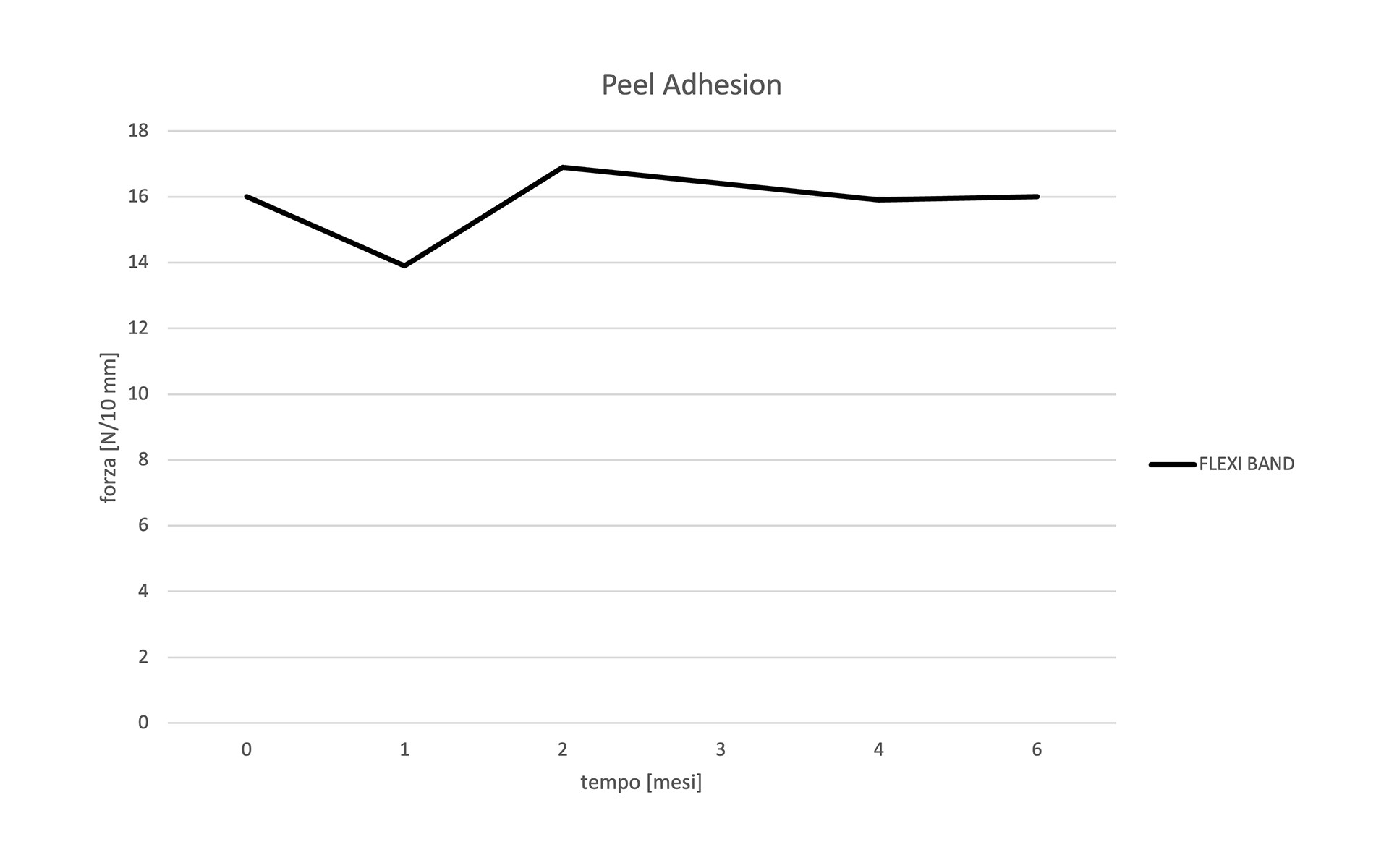
Adhesion strength tests
Adhesion tests for SPEEDY BAND confirmed excellent values, even after more than 12 months of UV exposure.
In terms of tensile strength and adhesion, SPEEDY BAND maintains the required levels (>50 N/25mm and >30 N/25mm) even after 6 months of UV exposure.
The combination of real-word exposure tests and subsequent laboratory tests demonstrates that FLEXI BAND and SPEEDY BAND adhesive tapes are able to confirm the durability data specified in their technical data sheets, even when exposed to particularly harsh environments.
The durability tests on tapes and membranes were conducted in collaboration with the Cracow University of Technology as part of the European MEZeroE project
Membrane ageing resistance
As part of the MEZeroE project, the Rothoblaas TRASPIR EVO UV 115 membrane was exposed to UV and heat to assess any potential degradation of its polymeric structure.
In addition to assessing the membrane’s durability, the specific aim of the study was to determine the following properties of the Rothoblaas membrane:
1.Tensile properties - longitudinal direction according to EN 13859-1.
2.Resistance to tearing - longitudinal direction according to EN 13859-1.
3.Resistance to artificial ageing by exposure to UV and heat in accordance with the requirements of EN 13859-1. Durability diagnostics related to ageing included properties not defined in the standard. The tests included:
Observation in optical microscope – before and after ageing,
Observation in scanning microscope (SEM) – before and after ageing,
FTIR analyses – before ageing,
UV and heat ageing according to EN 13859-1, Annex C, with modification to 5000h,
FTIR analyses – after 1000h, 2000h, 3000h, 4000h and 5000h UV ageing,
FTIR analyses – after UV and heat ageing.
What the laboratory tests reveal
Durability under artificial ageing by UV and heat exposure
The report from the MEZeroE project includes the results of durability tests on the TRASPIR EVO UV 115 membrane, assessing its condition before ageing, after UV ageing and following combined UV and heat ageing. These tests were conducted on both the top layer (TOP) and on the bottom layer (DOWN).
The artificial UV ageing process involved exposing the samples to UV-A340 fluorescent lamps for 5,000 hours. Following UV exposure, the samples underwent thermal ageing, which entailed heating at 70°C for 2,160 hours after the initial 5,000-hour UV exposure.
Tests on both the reference (non-aged) and aged samples included observations using optical microscopy (OM), scanning electron microscopy (SEM) and fourier-transform infrared spectroscopy (FTIR) measurements. Additionally, FTIR analyses were carried out after 1,000, 2,000, 3,000 and 4,000 hours to monitor the degradation processes of the tested membranes during UV exposure.
The exposed surface of the membrane displayed micro-cracks after UV exposure, however the damage did not compromise the original properties of the adhesive film on the underside.
Figure 31 and Figure 32 show the microstructure of TRASPIR EVO UV 115 after UV and heat exposure, for the TOP and DOWN layer respectively.
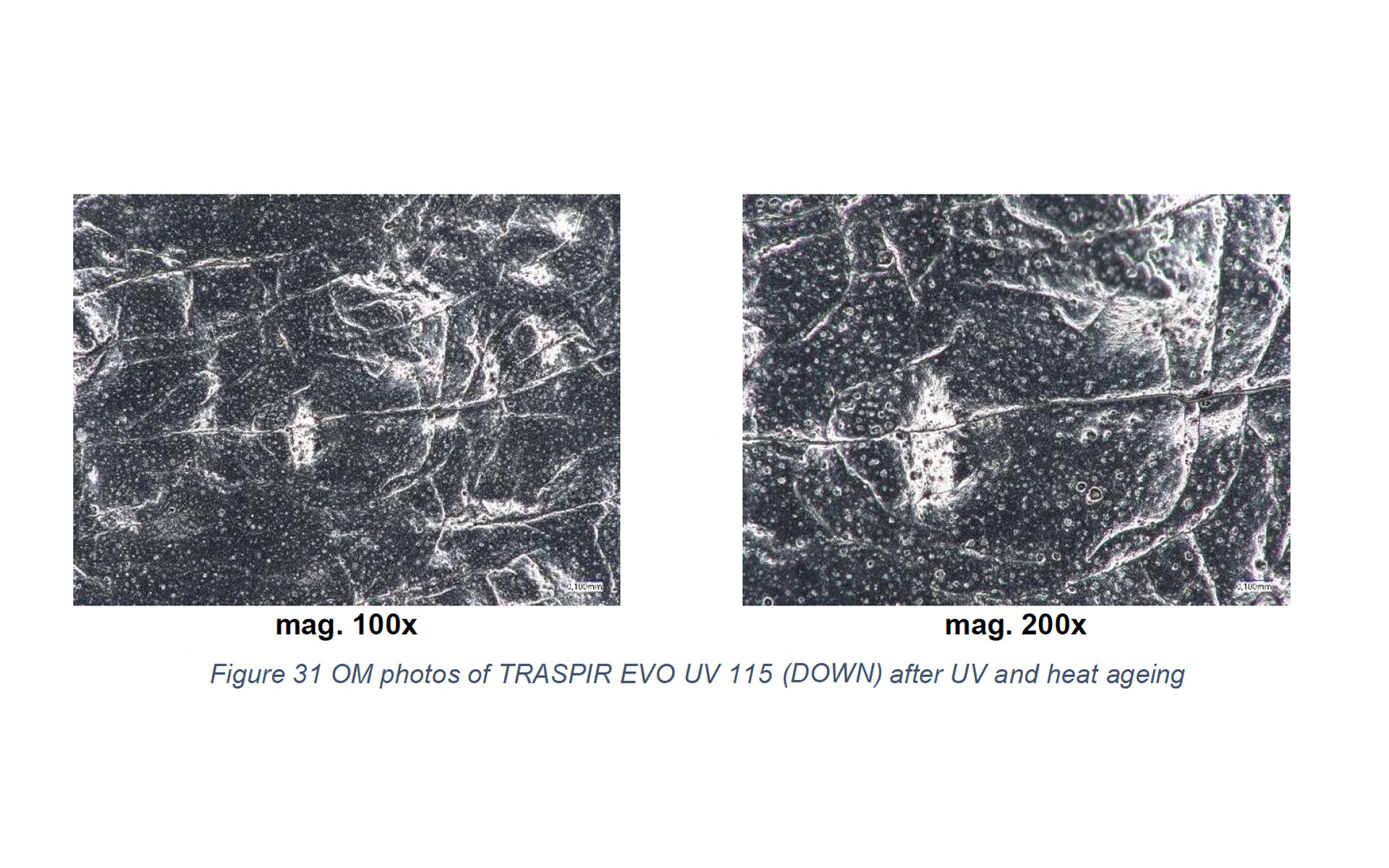
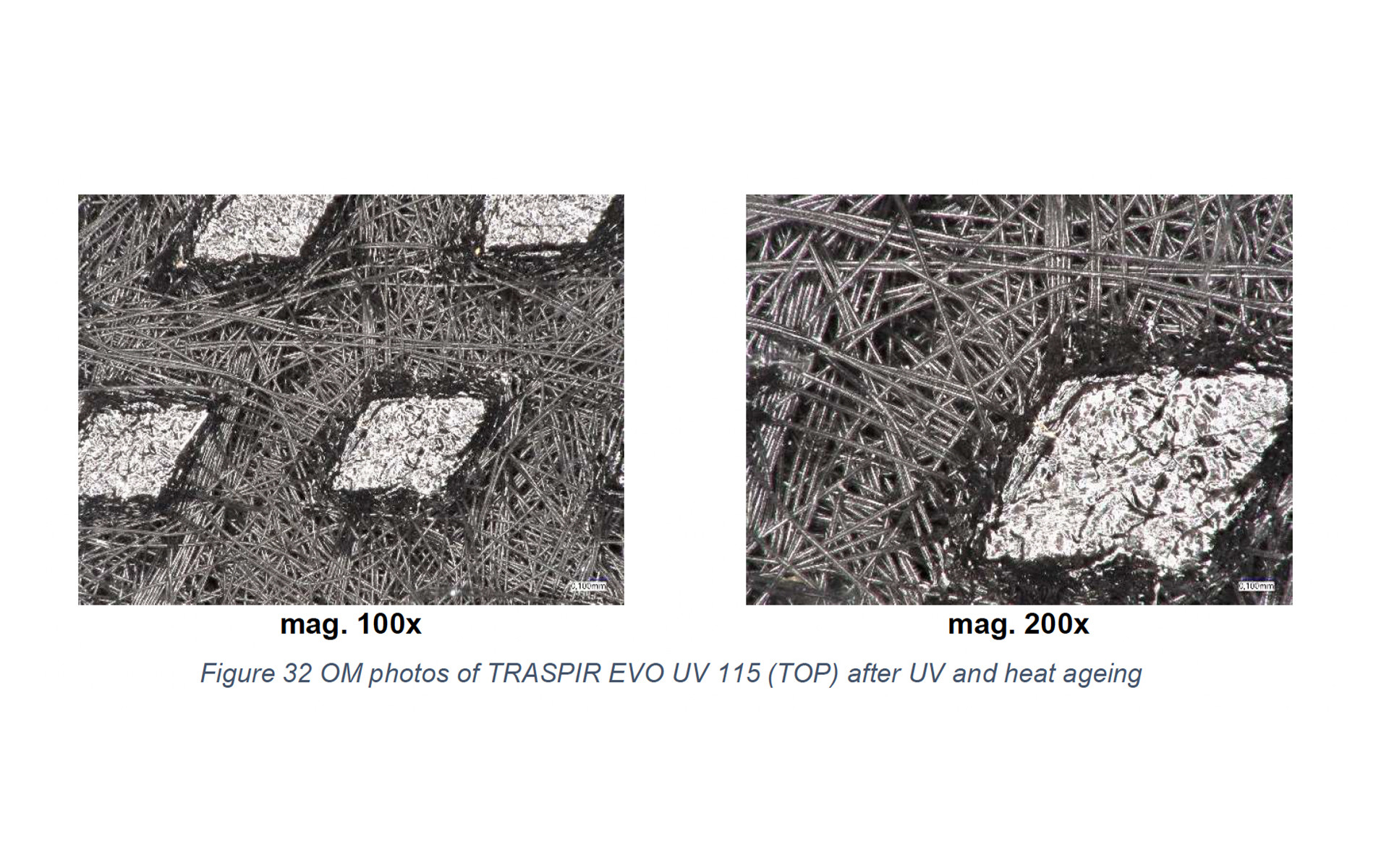
Optical microscope observations showed that exposing the TRASPIR EVO UV 115 TOP membrane to high temperatures intensified the degradation processes that had begun during UV exposure. The cracks formed during UV exposure further propagated and became more visible, indicating material degradation.
The tests and microscopic observations made it possible to identify and understand the degradation processes affecting the surfaces.
The FTIR measurements for the TRASPIR EVO UV 115 (DOWN) membrane before ageing, after UV ageing and following combined UV and thermal ageing are shown in the graph below.
The exposed surface, consisting of the non-woven fabric layer (TOP), degrades but continues to protect the functional PU layer of the membrane (DOWN).
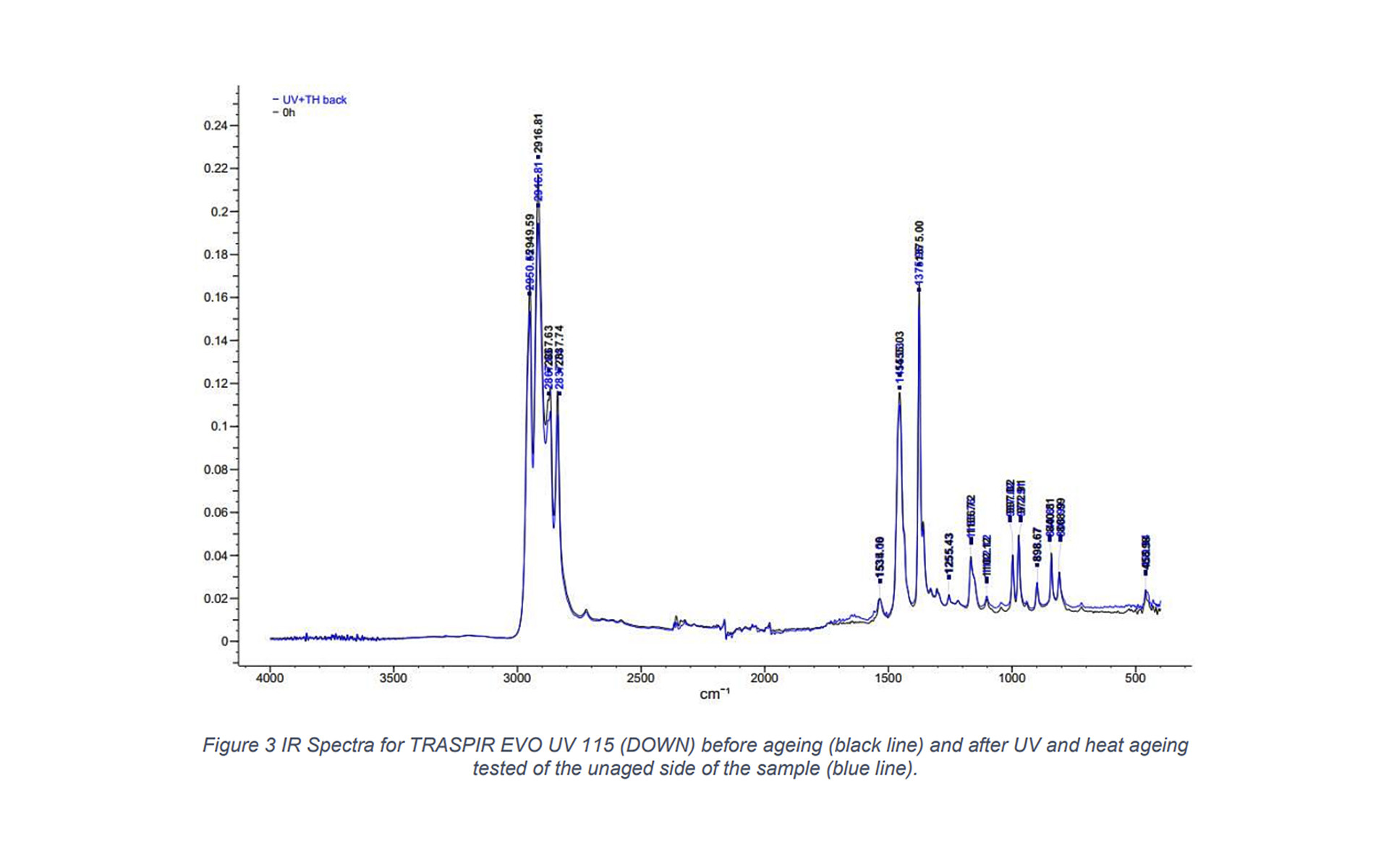
The graph shows that there are no substantial changes in the physical-chemical structure of the functional film.
Ageing resistance of membrane-tape-membrane joints
The purpose of this test was to determine the resistance of membranes and tapes to artificial ageing processes by UV and heat exposure, in accordance with the requirements of EN 13859-1.
Two types of joints were tested:
TRASPIR EVO 160 + SMART BAND + TRASPIR EVO 160
TRASPIR EVO UV 115 + FLEXIBAND UV + TRASPIR EVO UV 115
The simulation of the test conducted to demonstrate the durability of the TRASPIR EVO 160 + SMART BAND + TRASPIR EVO 160 joint, can be found here:
https://www.youtube.com/shorts/jvcqfUrTL6k
On the left, the tape had been in a conditioned connection for 20 hours (the time required for a newly applied product to settle, as specified by the standard); on the right, the tape had been conditioned and "aged" for 300 days, resulting in noticeable discolouration.
The joint consisting of the TRASPIR EVO 160 membrane and the SMART BAND universal single-sided adhesive tape is extremely durable even after ageing.
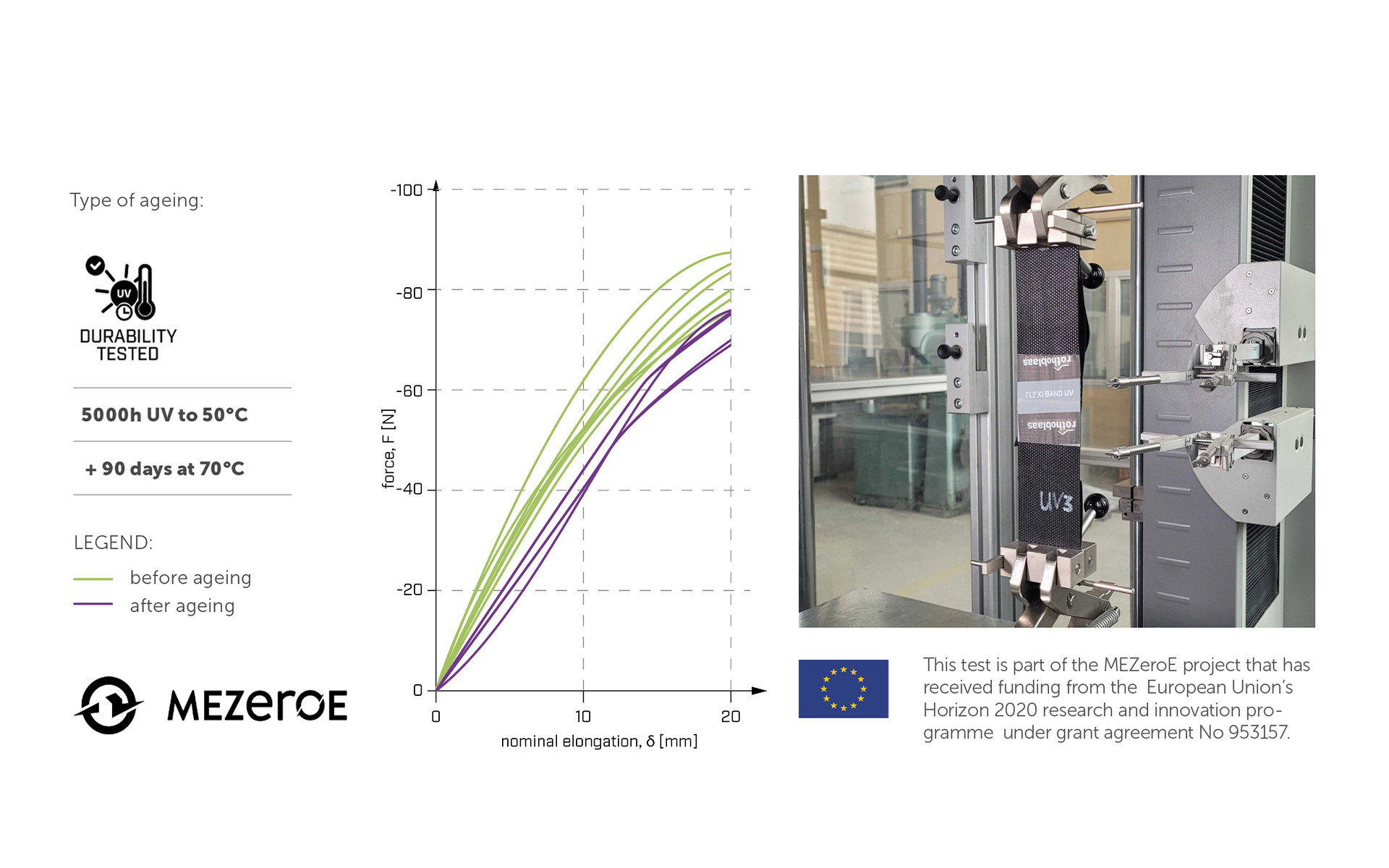
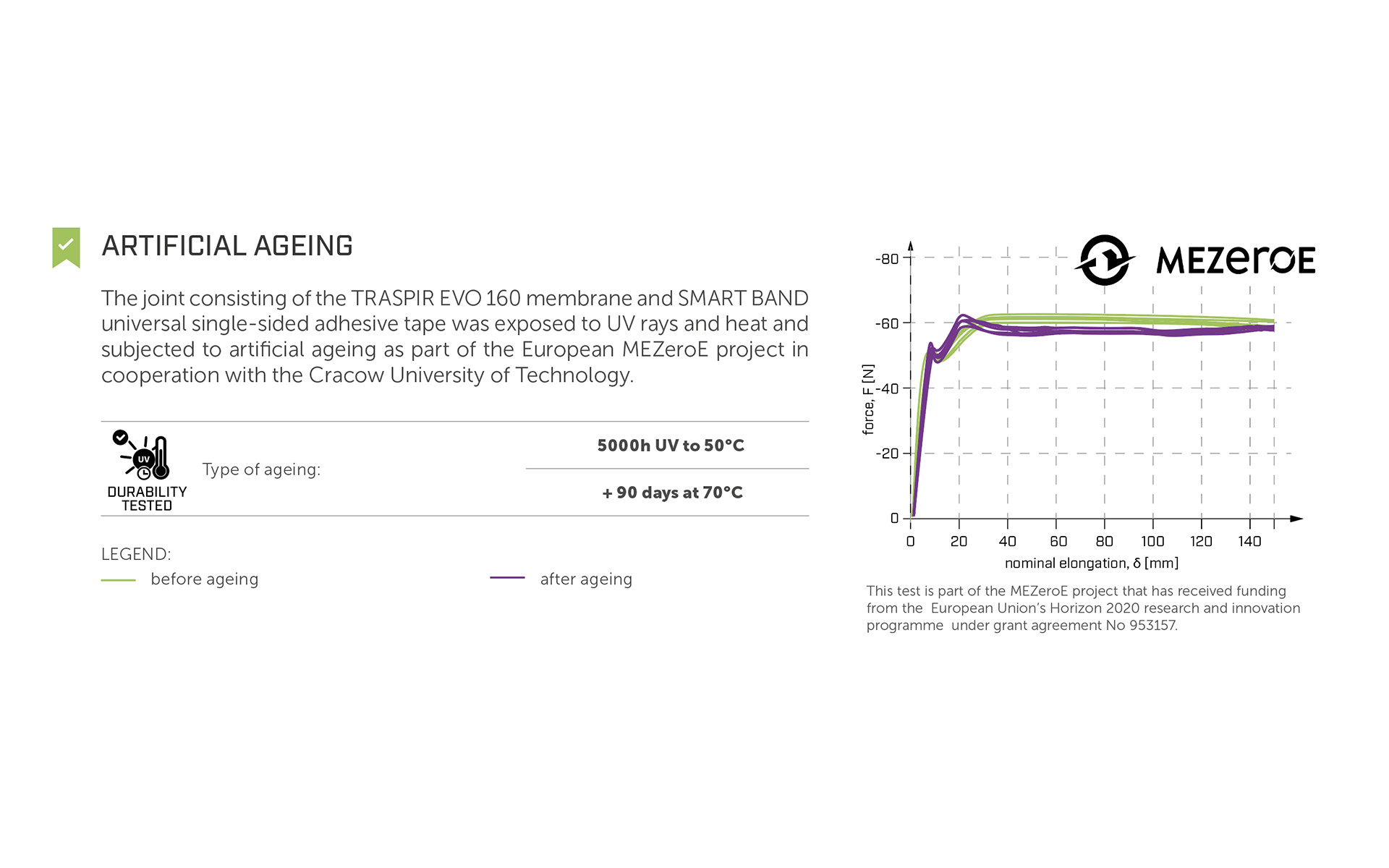
Both joints retain their maximum shear strength after ageing.
Durability of a membrane on a CLT wall: a real case study
During the expansion of the Rothoblaas headquarters, the building's main façade was completely dismantled. The modules were comprised as follows: CLT panels, insulation, TRASPIR EVO UV 210 and the cladding substructure. To assess the functionality of the façade and evaluate its potential for reuse, the membrane’s water tightness and mechanical performance were tested, showing that after 5 years of use, they had remained completely intact.
The percentage indicates the retention of the membrane’s mechanical properties after 5 years.

Why choose durable products
Investing in durable products is not just a commitment to quality but also a smart, long-term strategy – an investment in the future of your buildings:
Resistant to weathering: The tested tapes demonstrated excellent performance even under extreme conditions, such as those in Florida.
Designed to last: Extended accelerated ageing tests have shown that certain products maintain their adhesive and mechanical properties over time better than others, exceeding standard regulatory requirements.
Cost-effective: Choosing durable materials reduces the need for frequent replacements, lowering long-term costs related to maintenance and the purchase of new materials.
Lower environmental impact: Long-lasting products contribute to greater sustainability by reducing waste production and the environmental impact associated with the production and disposal of less durable materials.
If you're looking for durable solutions, you can find them here: “TAPES, MEMBRANES, SEALANTS AND FIRE PROTECTION – 2024”
*MEZeroe:
This test is part of the MEZeroE project that has received funding from the European Union’s Horizon 2020 research and innovation programme under grant agreement No 953157.
Reprodução reservada
Technical Details
- Year:
- 2024
- Companies:
- Rothoblaas, Cracow University of Technology
- Country:
- Any
- Produtos:
- SPEEDY BAND FLEXI BAND FLEXI BAND UV SMART BAND TRASPIR EVO 160 TRASPIR EVO UV 115 TRASPIR EVO UV 210 TRASPIR EVO 300